Your challenges
in Non Destructive Testing
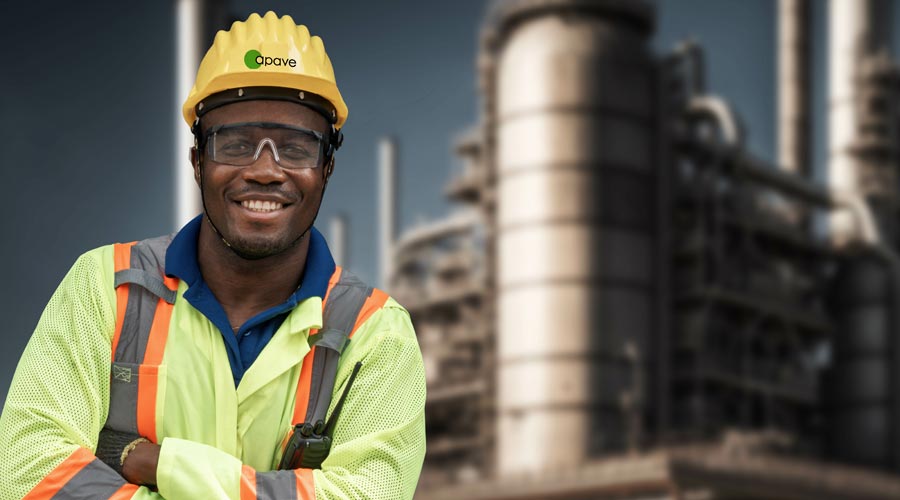
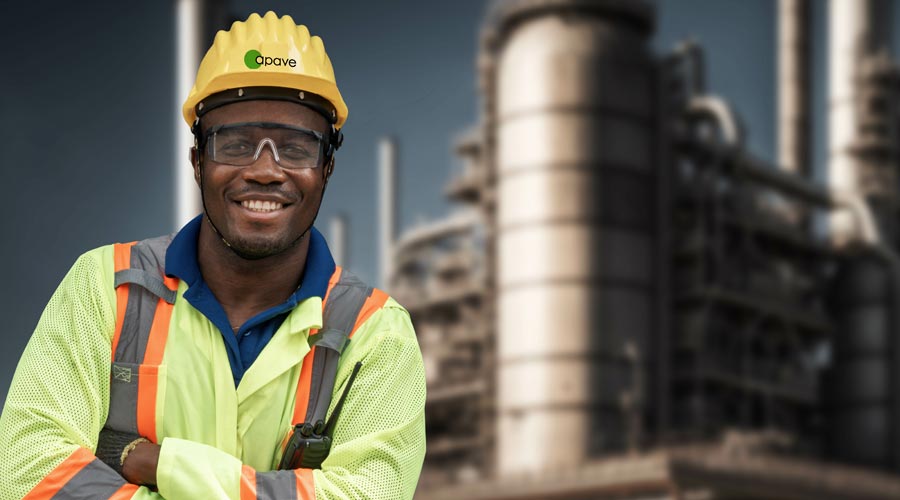
Preserving the integrity, reliability and health of your equipment, structures and installations from the design stage and throughout their lifecycle is essential to optimising your operational performance, reducing breakdowns and guaranteeing user safety. Non-destructive testing is a high-performance method for detecting and characterising the slightest defect without risking damage to the target.
This service is not available in Tunisia.
Contact us
Apave solutions
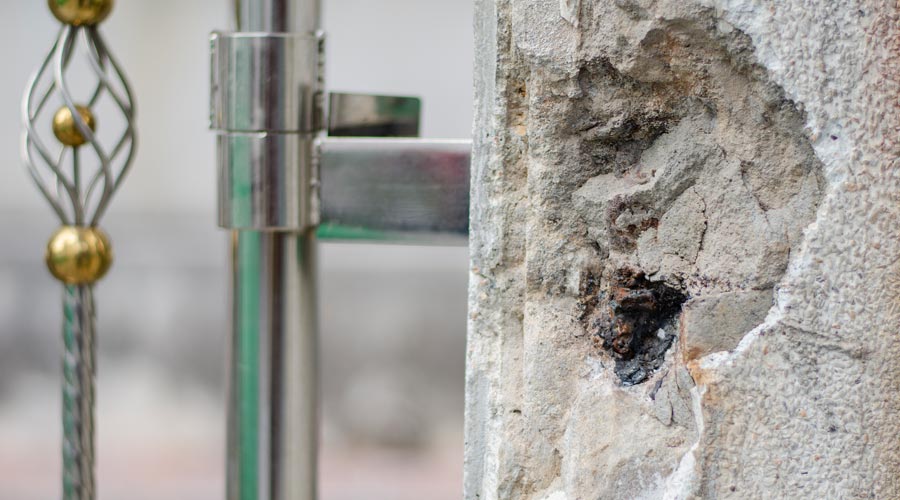
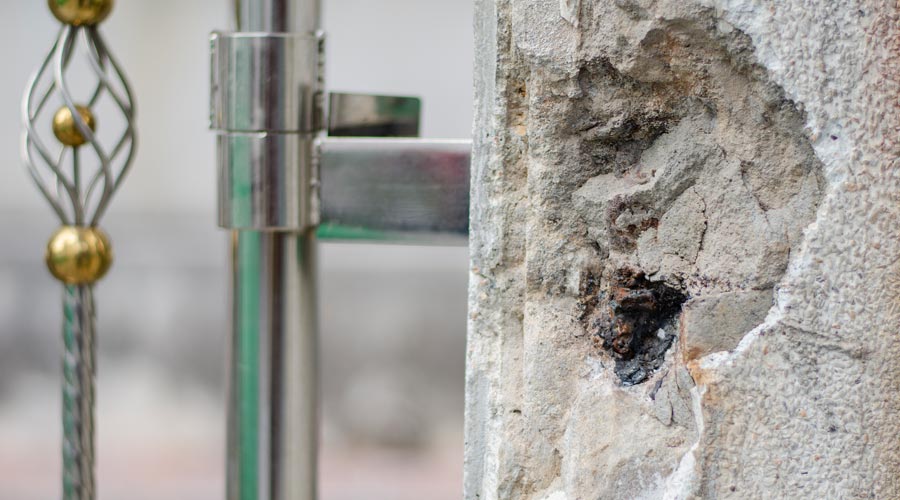
Apave is able to carry out all types of non-destructive testing, using proven methods and innovative technologies to meet your challenges:
- Traditional non-destructive testing methods: dye penetrant testing, magnetic particle testing, radiography, ultrasound, television inspection.
- Advanced non-destructive testing methods: ultrasonic techniques, Alternating Current Field Measurement (ACFM), EMAT, Time of Flight Diffraction (TOFD), Cobra, etc.
We can also carry out non-destructive testing by visual inspection using drones, to work in narrow or high places that are difficult to access.
We can carry out non-destructive testing on all types of materials, structures, equipment or installations, whether new or in operation, such as:
- Welds
- Metallic materials
- Storage tanks
- Boilers
- High-temperature enclosures
- Pipes, tubes, pipelines and pipework
- Bolted assemblies
- ...
Non-Destructive Testing methods
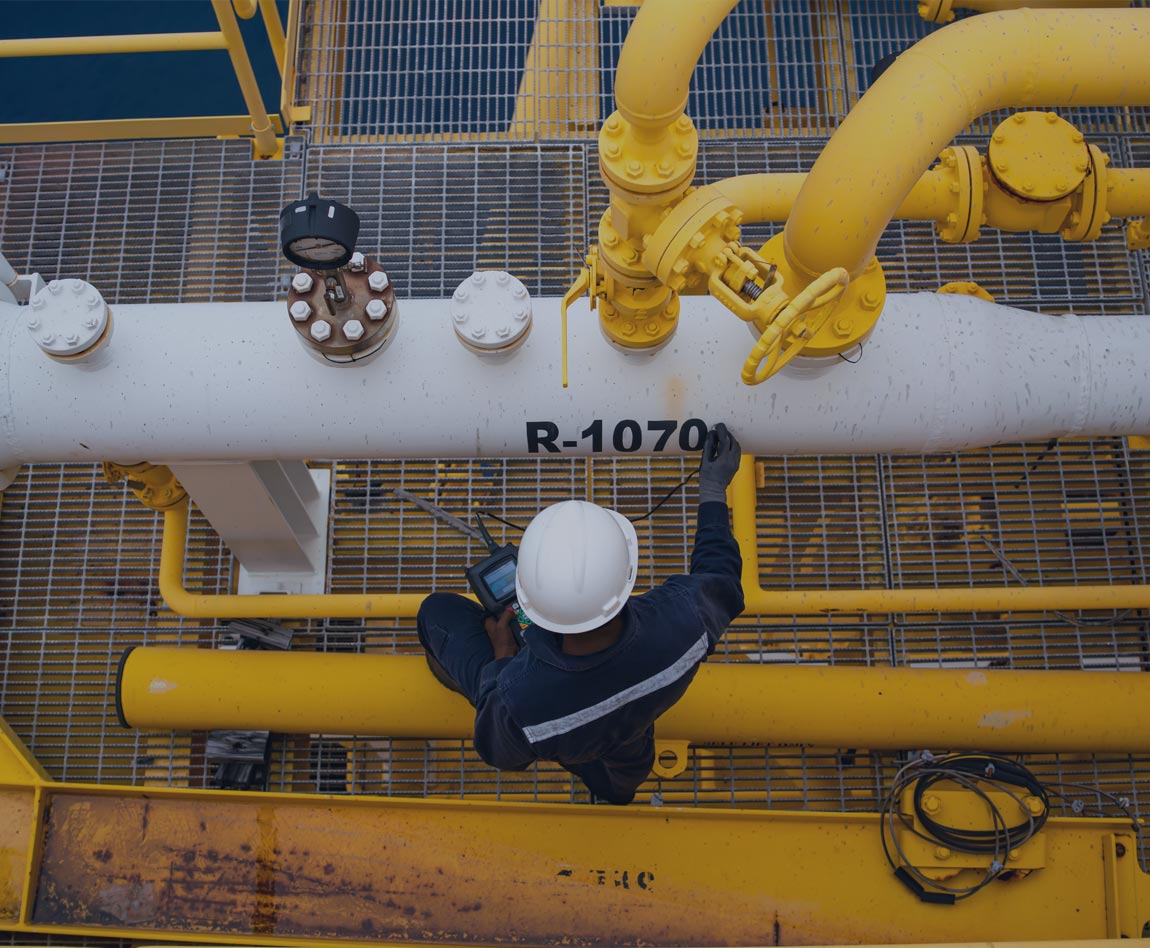
Apave's expertise
In Africa, Apave has a large network of experts with proven know-how, a wide range of innovative tools and a track record of working with key players across the continent. We are committed to providing a fast, tailor-made service in the shortest possible time. Together, we identify the non-destructive testing method best suited to your needs and the type of structure or equipment involved. Our multidisciplinary team and modern processes enable us to identify anomalies and structural defects with the utmost accuracy and precision, whatever your sector of activity (aeronautics, automotive, aerospace, rail, nuclear, energy, etc.). |
A solid territorial network in Africa
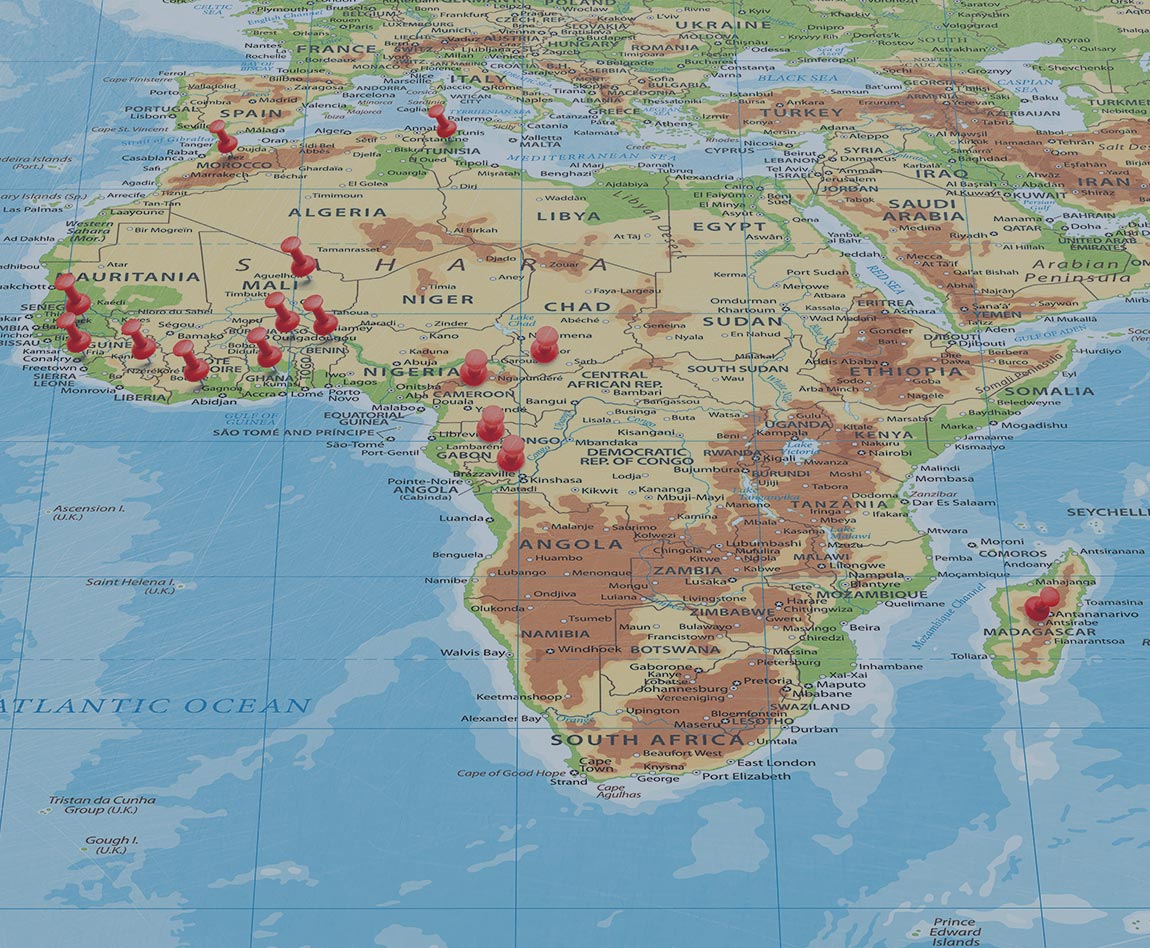
Your questions
about our NDT services
-
What is non-destructive testing (NDT)?
Non-destructive testing (NDT), also known as "non-destructive evaluation" or "non-destructive testing", is a set of methods used to assess the condition of structures, equipment or installations, without risking damaging them. These inspection methods make it possible to detect, locate, size and characterise all external and internal defects on all types of sensitive materials and to monitor their development, using non-damaging tools and methods. NDT is the opposite of destructive testing (mechanical testing, metallographic testing, etc.), which inevitably damages materials during examination. -
When should non-destructive testing (NDT) be carried out?
Non-destructive testing can be carried out throughout the operation of plant and equipment, to anticipate ageing and to check their condition periodically. It can also be carried out as part of maintenance, if a malfunction has been identified, for example. NDT can therefore be carried out at any stage in the life of a structure or piece of equipment: manufacture, operation, repair, predictive or preventive maintenance, etc. -
What are the different types of non-destructive testing?
Non-destructive testing can take several forms. For example, it can take the form of :
- - a visual inspection (VT), for example, which consists of checking the external condition of a part to detect obvious defects
- - radiological inspection (RT) to analyse the inside of materials using X-rays
- - magnetic particle inspection, which involves spraying a magnetic powder onto the material, which accumulates in cracks and open cavities
- - penetrant testing (PT): this method involves inducing a liquid to penetrate the material, which will highlight the cracks in the structure
- - ultrasonic testing: by transferring an acoustic wave through the material.
- - ...
-
What are the advantages of non-destructive testing?
Non-destructive testing enables the whole of a material to be inspected with the highest level of precision, and all internal and external defects to be detected. It's a non-damaging method that enables a diagnosis to be made in real time and the evolution of the material to be monitored over time to ensure its long-term integrity. It is a rapid test that also makes it possible (depending on the process chosen) to locate, size and characterise defects so that appropriate corrective action can be taken. NDT can even avoid the need to dismantle or move a part. It is a particularly useful method in certain sectors requiring rigorous checks on manufactured parts (aeronautics, aerospace, railways, nuclear, automotive, etc.). -
What defects can be detected using non-destructive testing?
Non-destructive testing (NDT) can detect several types of external and internal defects: holes, cracks, open cavities, signs of wear, porosity, changes in thickness, etc. This makes it possible to anticipate the ageing of materials, detect the slightest flaw upstream and take appropriate corrective action.
Discover
our news